Production Process – “NifeliZ Standard”
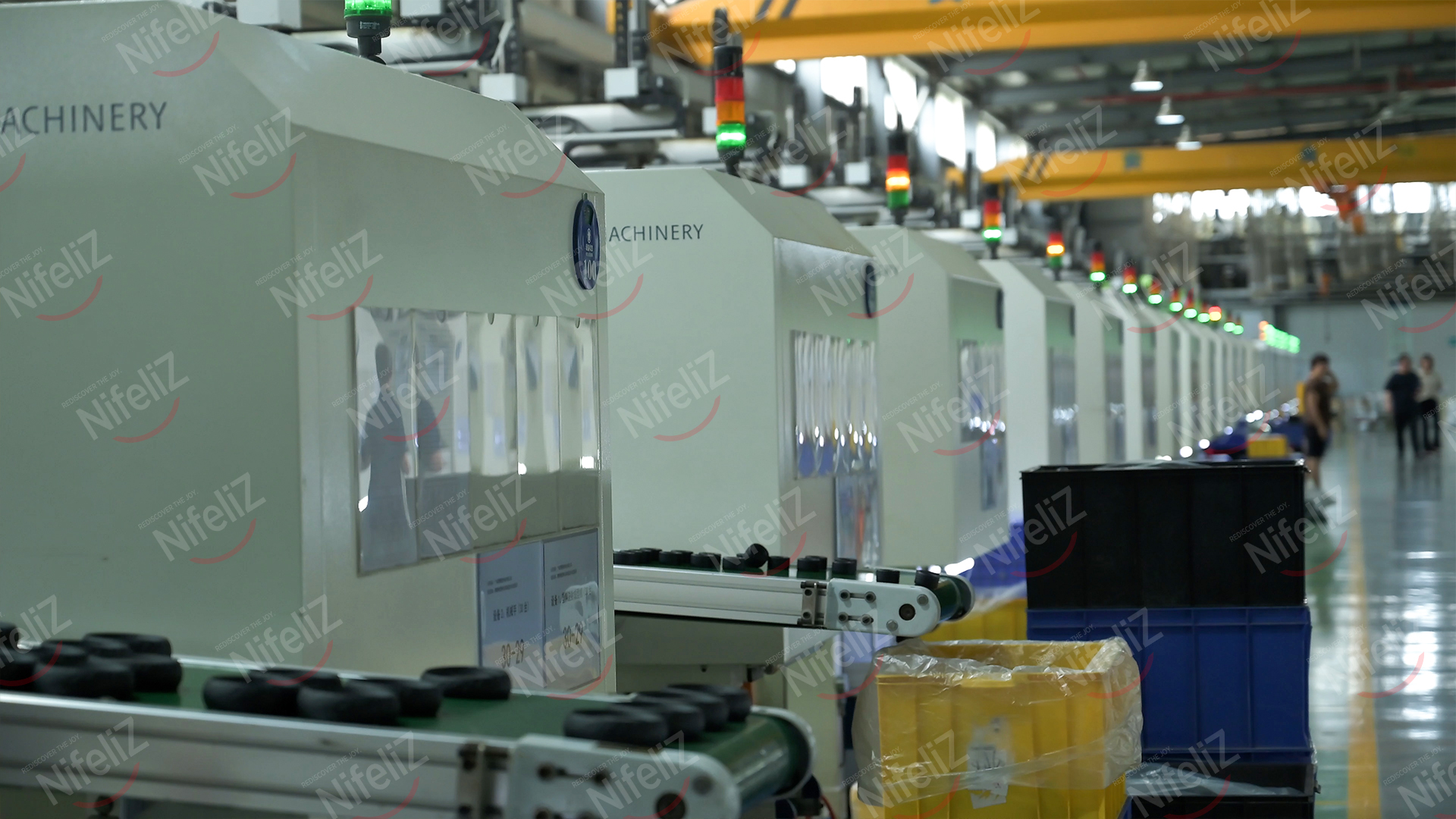
At NifeliZ, our slogan is “Rediscover the Joy.” We believe that the “joy” users experience from building our products comes from various factors, including product quality, the clarity of instructions, and the final display of the completed model. Quality is the foundation, just like the base of a building—only with a strong foundation can the structure above be vibrant and beautiful.
Our factory is located in Shantou, Guangdong Province, China, a coastal city. The main factory covers over 250 acres, dedicated to the development, design, and production of toy bricks.
Step one – involves the central feeding system, which transports raw materials (plastic granules) through overhead pipes throughout the workshop to each injection molding machine. In our first production workshop, we have 60 of these machines.
During peak seasons, the total weight of raw materials consumed by our three workshops in a month reaches 600 tons. The color of these raw materials is pre-mixed by specialized personnel according to product requirements and is referred to as “masterbatch.” This masterbatch is stored in silos outside the workshop, with each silo having a storage capacity of 30 tons.
Step Two – In our integrated injection molding machines, the main process involves heating the mold, injecting the plastic, and cooling the product into its final shape. Once formed, the finished pieces are trimmed, and the remaining “plastic twigs” (excess plastic) are recycled by crushing them to increase material utilization.
In this stage, our production speed reaches 3,000 sets of molds per 24 hours, with each set representing one full mold plate. The output quantity depends on the number of parts per plate. We opt for higher-quality equipment, which, though more costly, offers greater stability in pressure and consistency in the final products. Additionally, the heating and cooling processes during injection molding are faster, resulting in improved production efficiency and higher-quality finished products.
In our “NifeliZ Standard,” we use five methods to ensure the quality of parts produced during manufacturing:
This rigorous process guarantees high product quality and consistency.
The third step – the parts sorting. We use the latest fifth-generation visual inspection equipment, automation, and optical sensing technology to achieve the classification of parts. The parts pass through the inspection area, and high-speed cameras and optical sensors scan and determine the shape, color, and quantity of the products, and automatically remove non-standard parts. It is more accurate and efficient than the original fourth-generation infrared inspection equipment.
The final step is packaging. Together with the sorting machine, the parts sorted by the system are packaged through the conveyor belt and sub-packaged using heat shrink film technology. Our large code is printed on the packaging, which is convenient for end customers to intuitively distinguish the parts they need to use during assembly. Multiple plastic bags are packed into color boxes with designed patterns and finally sealed.
At the end, we still have a quality inspection step, and the finished product passes the final inspection to ensure that the packaging is correct. It ensures that our products meet the standards and can remain in good condition during transportation.
These steps, our “NifeliZ Standard” ensure the quality of our products and the satisfaction of our customers.
Rayvowen at 5:24 pm, November 19, 2024 -
And after all that you are still missing pieces when the model is delivered and no answer to my emails requesting the missing pieces
尼费利兹_adm at 8:42 pm, November 19, 2024 -
Thank you for reaching out, and we sincerely apologize for the inconvenience caused by the missing pieces and the delay in responding to your request. Due to a high volume of recent orders, our response time has been slightly longer than usual, but please rest assured that we are prioritizing your issue.
Alan at 4:56 pm, January 13, 2025 -
Model Assembly
尼费利兹_adm at 8:13 pm, January 13, 2025 -
Thank you for taking the time to read about our factory! Model assembly is a key part of our process, and we’re thrilled to share how much care and precision goes into creating each set. If you have any questions or thoughts about our models, we’d love to hear them! 😊